FGT think your best choice in the future
System Integration Designers in FGT
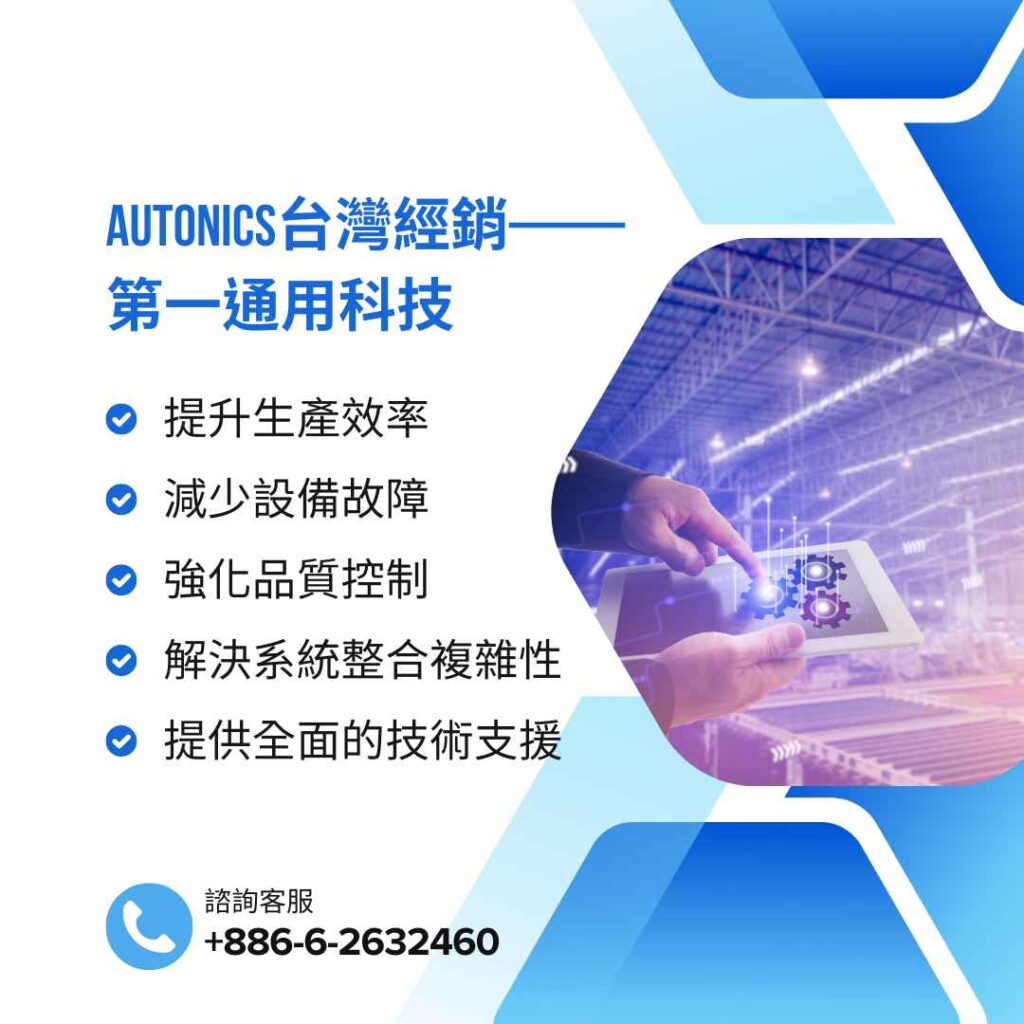
- 2025-03-13
- 3:26 pm
Improving production efficiency and reducing failure rates: Autonics Taiwan distributors help companies strengthen their competitiveness
As the global manufacturing industry moves towards intelligent and high-efficiency production models, industrial automation has become a key factor in enhancing corporate competitiveness. Issues such as equipment stability, production line efficiency, quality control, and system integration directly affect a company’s operational performance and market competitiveness. As a world-leading automation brand, Autonics provides efficient production equipment for the manufacturing industry with its advanced sensing technology, precise control systems and intelligent solutions.
作為 Autonics 在台灣的經銷商(原台灣autonics代理),第一通用科技擁有超過 20 年的 PLC 自動化機電工程設計經驗,是台灣最早期引進韓系自動控制廠牌的專業進口商。第一通用科技結合 Autonics 的核心技術,提供從設備選型、技術整合到生產優化的一站式服務,助力企業強化競爭力。
Autonics' core brand advantages and technical support
Autonics 產品涵蓋光電感測器、近接感測器、步進馬達控制器、雷射打標系統等完整自動化解決方案,其多款產品獲得 iF、RedDot 等國際設計大獎,技術創新性與穩定性兼具。Autonics 擁有 13 家國際分公司與生產基地,透過台灣經銷商——第一通用科技(原台灣autonics代理)提供在地化技術支援,確保設備的快速導入與即時維護。
Technological leadership and complete product matrix
Autonics product technology covers multiple fields and is suitable for industries such as precision manufacturing, semiconductors, mechanical processing, and automobile manufacturing, and can achieve cross-industry applications:
- Photoelectric sensor: Accurately detect the position and movement status of objects to improve production line stability.
- Proximity sensor: ensures the accuracy of parts assembly and improves the degree of equipment automation.
- Stepper motor controller: Enhance equipment motion accuracy and improve production consistency.
- Laser marking system: suitable for precision marking and engraving, improving product identification and traceability.
Global resource integration and localized services
Autonics has international production and R&D resources, combined with First General Technology's local services, to provide Taiwanese companies with high-performance technology upgrade solutions.
Improving production efficiency: Application of Autonics sensors and controllers
In modern factories, increasing productivity is not just about speeding up machine operations, but about making equipment work together in a smarter way and reducing waste. First General Technology helps companies optimize their production processes by introducing Autonics high-precision sensors and intelligent control systems.
1. Sensing technology optimization process
Through Autonics' high-precision photoelectric, temperature and pressure sensors, the production line can monitor every key link in real time. For example, in the electronics manufacturing industry, temperature sensors can ensure the stability of the welding process, avoid poor solder joints due to temperature fluctuations, and improve product yield.
2. Controller collaborative upgrade
Through the deep integration of PLC and motion control equipment, the production line can adjust the operating speed and rhythm according to real-time data. After the introduction of the system in a certain automobile parts manufacturer, not only did the production capacity increase by 15%-30%, but the coordinated operation between equipment also reduced the idle time of machines by about 20%.
3. AI-assisted decision-making system
The automation system not only makes the equipment "move", but also makes the equipment "smarter" through AI intelligent analysis. First General Technology integrates AI technology with Autonics equipment data to create a smart decision-making system.
Equipment load prediction: Analyze historical data through AI algorithms to predict equipment load, allowing production plans to be adjusted dynamically. For example, a semiconductor production line used AI to monitor equipment operation data and predicted the possible overload risk of the machine in advance, successfully reducing the sudden downtime accidents of 40%.
Smart production scheduling adjustment: Not only does the machine need to operate stably, the scheduling of the entire production line also requires intelligent management. The AI system can dynamically adjust production schedules based on real-time order demand and machine status to maximize the factory's capacity utilization. For example, in the food packaging production line, through the cooperation of Autonics sensors and AI systems, the packaging speed is increased by 15% and the material waste is effectively reduced by 10%.
Through the integration of First General Technology's technology and Autonics' advanced automation technology, companies can make existing production lines more efficient without adding additional machines and equipment, ensuring that they maintain their advantages in the highly competitive market.
Reduce Equipment Failures: Autonics Predictive Maintenance Solutions
Equipment failure may lead to high maintenance costs and production interruptions. First General Technology provides Autonics predictive maintenance solutions to help companies improve equipment stability and ensure uninterrupted production. Based on actual application data, through preventive maintenance and real-time monitoring, the goal is to reduce the failure rate of customer equipment to below the industry average of 60%.
Preventive maintenance program
- Equipment health status assessment: Autonics' vibration sensors continuously monitor the vibration spectrum of key parts such as motors and gearboxes, which can predict possible faults such as bearing wear and shaft misalignment in advance; current sensors can analyze motor load changes and detect abnormal energy consumption conditions, such as overload problems caused by belt slippage, allowing maintenance personnel to respond immediately.
- Equipment self-diagnosis function: The sensor regularly generates equipment health reports, replaces worn parts in advance, reduces sudden failures, and ensures stable operation of the production line.
- Maintenance strategy optimization: Through the analysis of historical sensor data, establish equipment life model and formulate accurate maintenance plan. For example, when the AI system detects that the lubricant may reach a critical point within two weeks, the system can automatically issue maintenance reminders to ensure smooth operation of the machinery and extend the service life of the equipment.
- Remote monitoring platform: Monitor abnormal conditions through IoT data and send maintenance alerts in advance to reduce the risk of unplanned downtime and improve equipment availability.
Localized technical support
First General Technology provides 24-hour technical support and combines Autonics' original resources to establish a complete rapid response mechanism, shortening the equipment repair time (MTTR) to 4 hours to ensure stable production operation.
Strengthening quality control: Application of Autonics vision inspection system
Quality control is a key step in the production process. Autonics provides high-performance visual inspection systems to improve product yield.
- Fiber optic sensors: used for wafer inspection to improve the accuracy of semiconductor manufacturing.
- Photoelectric sensors: Improve the stability of automotive welding, spraying and other processes.
- Image analysis system: improves the accuracy of defect detection in food and 3C electronic products.
Solving the complexity of system integration: Autonics product compatibility and ease of use
In an industrial automation environment, the challenge of system integration comes not only from the compatibility between different devices, but also requires efficient data management and intelligent decision-making. Autonics products are highly compatible and can be seamlessly connected to various industrial control equipment. They can also improve the accuracy of production decisions through intelligent data analysis.
1. Deeply integrate SCADA/MES systems to improve data management and decision-making capabilities
Autonics sensors and control systems can be seamlessly integrated with MES (Manufacturing Execution System) and SCADA (Supervisory Control and Data Acquisition System), allowing companies to grasp complete production data and further optimize the decision-making process.
Real-time data upload: Sensor data is transmitted to the MES system in real time to generate a production efficiency heat map, helping companies quickly identify production line bottlenecks and find inefficient links.
AI intelligent analysis: Through AI algorithms, historical data is analyzed to automatically recommend the best equipment parameter combination. For example, in a plastic injection molding production line, the system can dynamically adjust the injection temperature and pressure according to the characteristics of different batches of raw materials to ensure the stability and consistency of each product.
2. Optimize energy consumption management and create a green production environment
In the production process, energy management is a major challenge. How to reduce energy consumption and optimize equipment efficiency is an issue of concern to many companies. Autonics helps companies identify high-energy-consuming equipment and achieve optimal management through intelligent sensing and data analysis.
Power sensors monitor energy consumption: The system can monitor energy consumption in each link of the production line (such as air compressors, cooling towers, etc.), identify abnormal energy consumption points, and avoid unnecessary energy waste.
Intelligent energy-saving control: Combined with the Autonics energy management system, the equipment can adjust its operating mode according to actual production needs. For example, a factory optimized production power scheduling through this system and successfully reduced power consumption per unit product by 18%, which not only saved costs but also met the needs of environmental protection and sustainable development.
3. High compatibility and flexible expansion
In addition to data integration and energy-saving management, Autonics products also have extremely high flexibility in system compatibility, allowing enterprises to easily expand automation applications.
Supports multiple communication protocols (such as Modbus, EtherNet/IP) to ensure seamless connection with various control systems.
The modular design allows for flexible expansion according to the needs of different industries, and can be quickly introduced regardless of whether it is a small factory or a large-scale intelligent production line.
Through the professional distribution and technical support of First General Technology, Autonics can not only help companies overcome the difficulties of automation system integration, but also improve production efficiency and reduce energy consumption through data-driven intelligent decision-making, helping companies move towards a smarter and more sustainable manufacturing model.
Improving production efficiency and reducing failure rates: Autonics Taiwan distributors help companies strengthen their competitiveness
Industrial automation has become the key to improving the competitiveness of the manufacturing industry. From production line efficiency to equipment stability, companies are looking for the best solutions. As a global automation leader, Autonics provides precise sensing and intelligent control technologies to improve production efficiency and reduce equipment failure rates.
第一通用科技作為 Autonics 在台灣的經銷商(原台灣autonics代理),擁有 20 多年 PLC 自動化機電工程經驗,提供從設備選型、技術整合到生產優化的完整解決方案,助力企業強化市場競爭力。
What companies need is not just equipment, but a complete automation solution. Autonics uses precision sensing and intelligent control, combined with the technical support of First General Technology, to help Taiwan's manufacturing industry improve efficiency, reduce failure rates, and achieve smart manufacturing.
Whether it is machine tools, semiconductors, automobile manufacturing or food processing industries, Autonics and M1 can provide the best automation technology to help companies stay ahead in the global market.